Rickard Specialty Metals and Engineering Titanium Extrusions
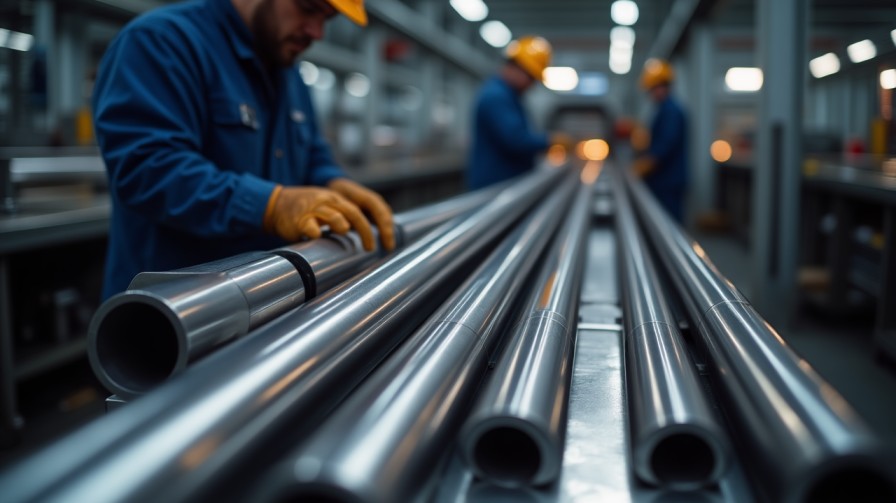
Titanium extrusions are used in a variety of applications in the aerospace industry from titanium engine pylons to titanium tracks for seats. The extrusion process brings a number of advantages over forging. Custom designed shapes, fine tolerances, less downstream machining, and less waste. Grade 5 Titanium bar or billet are used.
Titanium is extruded at a temperature range of 850 to 1150 degrees Celsius. Solid round titanium bar are induction heated to a specific temperature. Billets are heated then coated with powered glass compound that lubricates and protects the surface of the material, especially to retain the titanium matte finish free of alpha case.
At the extrusion press, each billet is hydraulically pushed through a die at pressure of up to 2000 tons, forcing the metal to configure to the die’s profile. The press can be adjusted to operate at high speeds, making operation of each extrusion in periods of time ranging from 1.5 to 5 seconds. The key to close-tolerance extrusions is obviously the quality and of the die. Instant failure of the dies is not unheard of, especially when the glass film breaks at high extrusion speeds.
The intense heat and pressure that affect extrusion dies generate interior erosion, informally called “die wash” that can cause dimensional tolerances to shift. Usually, the tolerances are maintained by inserting a new die for each item. After the shapes are extruded, downstream operations vary with the material.
The parts created by the extrusion process are usually heat treated so as to refine the grain structure.
Chemical treatment is used to remove any lubricant as well as the thin alpha case. This enhances machinability.
Whether it is a prototype, short run, or a long run, Rickard Specialty Metals and Engineering brings years of experience to the Titanium extrusion process.